负责人:曹宏瑞
所在学院:机械工程学院
一、项目简介
本项目针对航天舱体、飞机蒙皮、舰船螺旋桨叶片等大型复杂零件高精高效加工难题,研制与工业机器人相配套的智能主轴。主轴转速达20000r/min,径向跳动和轴向跳动小于 3μm,动平衡精度 G0.4。该智能主轴具备多传感信息感知、加工状态在线监测、异常辨识与自诊断、振动主动控制等功能模块,适用于铣削、钻削和磨削等加工,实现铣削轨迹精度和制孔定位精度均在 0.3mm 以内。
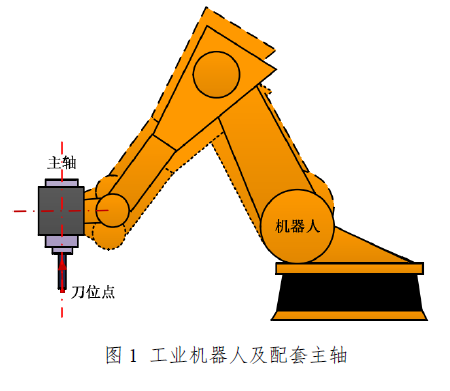
二、关键技术
本项目所研制的工业机器人高精高效加工配套智能主轴涉及的关键技术如下:
(一)智能主轴高刚性、轻质量设计技术
作为工业机器人末端执行器的智能主轴,高刚性、轻质量是其设计目标。在智能主轴动力学建模研究基础上,以减少主轴的动静态变形和提高主轴固有频率为目标,通过优化主轴轴承跨距、轴径、轴承预紧等参数,提高主轴刚性20%以上,质量减小15%。
(二)智能主轴多源信息精确感知与数据获取技术
智能主轴振动、切削力、温度等多源信息采集的难点在于狭小空间限制和高速旋转部件状态的直接感知与传输。提出柔性复合传感器(厚度小于2mm,测振带宽不低于20kHz,芯片面积小于5mm´5mm,无线供电与传输等)制备方法,实现振动、切削力、温度等信号的集成感知。
(三)智能主轴信号处理与加工异常状态辨识技术
融合现有传感器及柔性传感多源信息,提出稀疏监测指标构建新方法,构建时频域、阶次域、能量域内的早期异常预警指标,利用深度迁移学习缩小主轴不同运行工况、不同健康状态表征的差异性,对主轴在加工中颤振、尺寸超差、刀具破损等异常状态进行准确辨识,实现复杂多变工况下加工异常状态监测的漏报率和误报率不高于10%。
(四)智能主轴误差补偿与振动主动控制技术
研究控制器、作动器、主轴、切削过程之间的耦合关系,建立智能主轴切削颤振闭环控制系统,实现时变动态特性影响下智能主轴高速高效加工颤振的主动控制。将在线测量的切削力作为机器人结构刚度模型的输入,精确计算机器人末端位姿误差并补偿,实现铣削轨迹精度和制孔定位误差小于0.3mm。
三、应用市场
本项目研制的工业机器人配套智能主轴面向航天舱体、飞机蒙皮、舰船螺旋桨叶片等大型复杂零件高精高效加工。目前,这类大型复杂零件的加工主要依靠大型高性能多轴数控机床完成。大型精密机床非常昂贵,每台价格通常需要千万人民币,而且加工模式固定、配置复杂,通常不具备柔性和并行加工能力,也不具备可重构性,难以形成加工-测量一体化系统。工业机器人将逐步成为大型复杂零件加工的主要手段。
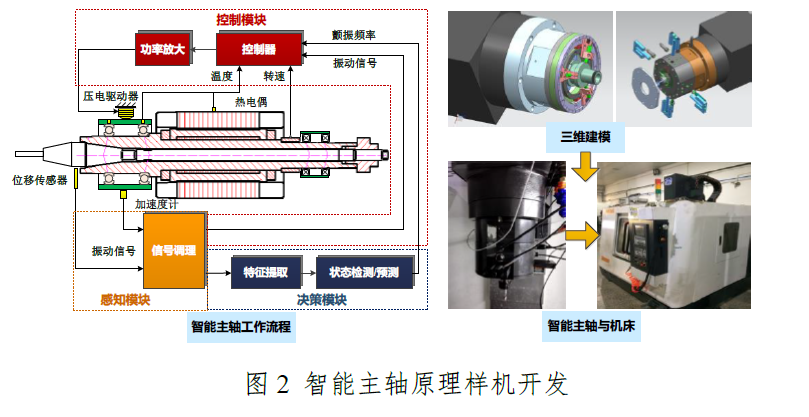
2020 年,我国工业机器人运营库存增长了 21%,累计安装量超过 80 万台,新安装量超全球新安装总量的三分之一。全球加工领域机器人约为5 万台左右,并连续两年保持超过7%的增长率不断增加。目前工业机器人在机械加工应用中多限于切边、去毛刺等轻载、精度要求不高的场合,鲜有应用于高精高效加工。本项目产品将在商用标准工业机器人的基础上,通过对主轴的智能化升级换代,解决工业机器人低精度、弱刚性与大型复杂零件高精高效加工之间的矛盾,具有广阔的应用和市场前景。
四、技术成熟度
□概念验证 □原理样机 □工程样机 □中试 □产业化
五、合作方式
□联合研发 □技术入股 □转让 □授权(许可)□面议